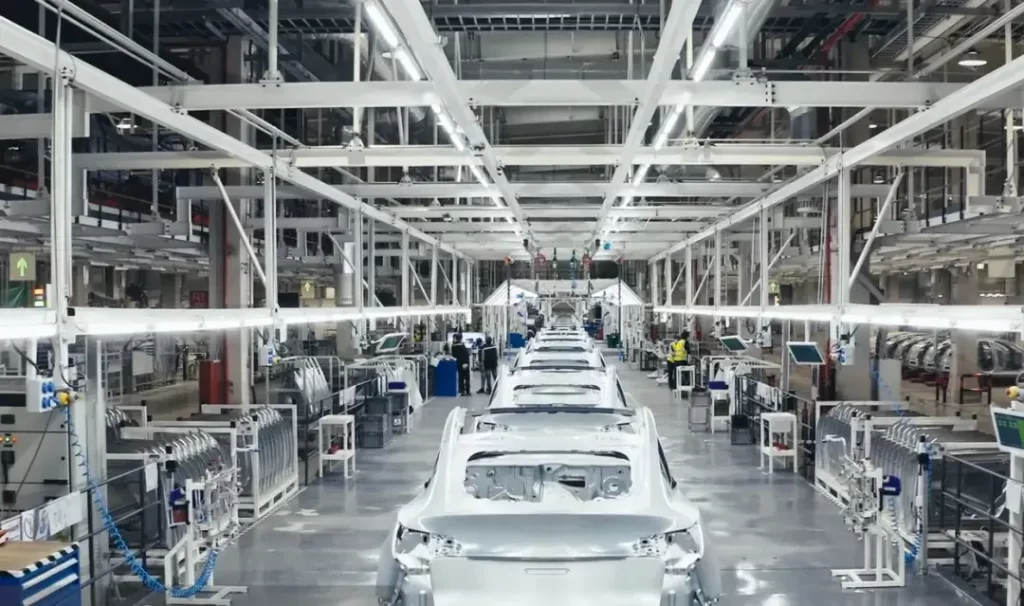
According to Nikkei, Toyota Motor Corporation will introduce integrated die-casting “Gigacast” technology for one-piece body parts at its plant in Aichi Prefecture in 2024 for prototyping of electric vehicle parts. Toyota is preparing for full-scale electric vehicle production by accelerating the introduction of the latest equipment, which can shape one-third of the body in three minutes.
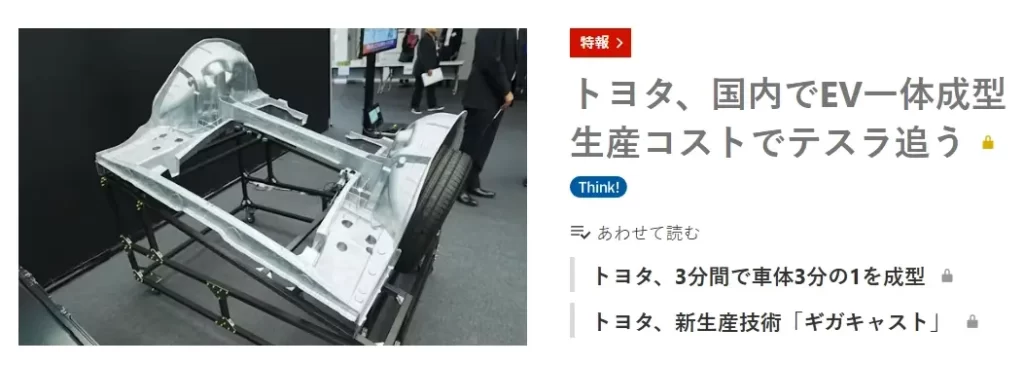
It is reported that Tesla pioneered the use of the unibody die casting process in the automotive industry and implemented it for the first time on the Model Y. After the adoption of integrated die casting technology for Tesla Model Y, the rear body manufacturing time can be reduced by 1-2 minutes from 1-2 hours, the Model Y cost can be reduced by about 40%, and the vehicle weight can be reduced by 10%.
The adoption of integrated die casting technology greatly simplifies the redundant process of automobile manufacturing and accelerates the efficiency of automobile manufacturing, which has brought tremendous changes to the manufacturing of traditional automobiles.
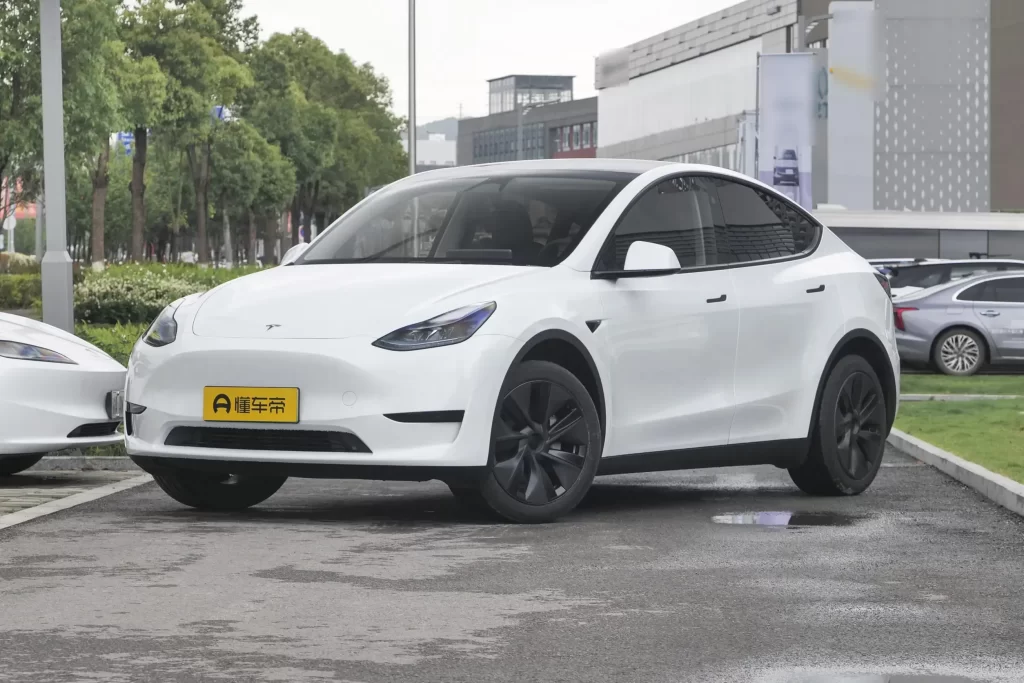
Some in the industry believe that Tesla’s proposed gigacasting (integrated die-casting) technology has set a new benchmark for automotive manufacturing, and can be said to replace the previously respected, “known for efficiency” Toyota production system.
Earlier, two Toyota executives revealed that nearly three decades after the launch of the first gasoline-electric hybrid, the Prius, the company is moving to convert most of the fuel models of Toyota and Lexus into pure hybrids, with the hope of eventually achieving “hybrid” of all models.